SAVING
THEIR SKILLS
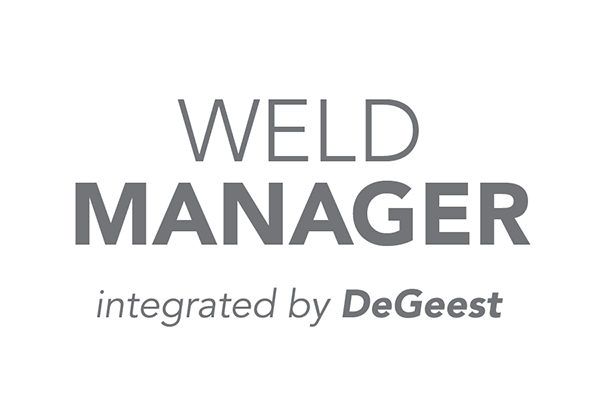
Weld Manager integrated by DeGeest
Create peace of mind and improve consistency by ensuring every part is welded using the correct wire and validated settings. Our manual welding solutions are designed to reduce human error and preserve legacy knowledge.
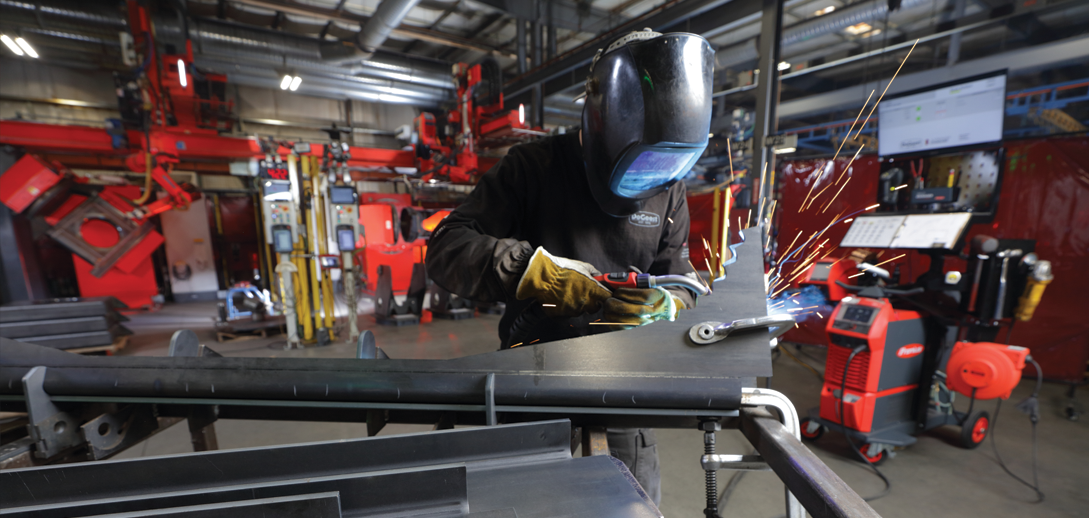
consistency is key. we can help.
A better way for manual welding technology to keep up with evolving quality standards or controls
As OEMs adapt to retiring baby boomers' decades of knowledge and skill, quality requirements are being raised out of necessity.
DeGeest experienced this and asked the question, "How do we retain the knowledge of our skilled people and create an easy way for the next generation to use it?"
Our R&D team partnered with Fronius to create an intuitive operator interface that combines the unique technology and software of both Fronius and DeGeest.
Introducing Weld Manager - Integrated by DeGeest
We've created the most technologically advanced shop-wide manual welding system in the world.
Weld Manager creates a system to ensure only validated PQR Weld Settings are tied to each unique part. The machine will not allow a welder to strike an arc unless all controls are met.
This allows you to have peace of mind knowing every welder is certified to weld a part using the correct wire and validated settings while the Fronius machine adapts wire speed and amperage for better welds.
The user interface also provides real time feedback for the operator and supervisors on target times, wire and gas usage.
Eliminating variables for greater consistency
Weld Manager is a revolutionary system that gives you control of something that was previously not possible.
Instead of spending time teaching new hires weld theory and machine settings, you can get them productive by training them on weld processes and sequences and not worrying if they have the right wire and settings required to build your parts.
Set target times, wire, and gas usage per part with tight tolerances
- Allows instant feedback to welders at their station if they are within the proper time and weld size
- Notifies supervisors if a job is completed outside of set parameters
- Gives welder and supervisor an opportunity to inspect parts
- Improves profits by identifying oversized or undersized or missing welds
Every welder and machine can be controlled to give you peace of mind that processes are followed to ensure parts meet quality requirements.
This technology also builds in automatic controls for management, quality inspectors, weld supervisors, weld leads and even operators.
By adapting technology to save your legacy weld knowledge, you can reduce the human error and inexperience that plagues many shops today.
DeGeest Corporation | Product Information